Quality and technology IN CONSTRUCTION
delivered with STRAIGHT communication
Predictive Maintenance: The Real Benefits of Smart Buildings That Know When Devices Will Fail
Artificial intelligence and IoT sensors are transforming building operations. Predictive maintenance reduces unexpected failures, saves energy, and extends the lifespan of building systems—provided that design and strategic thinking align with this technological shift.
CONSTRUCTIONSUSTAINABILITYTRENDAI ARCHITECTURE
Dr. Toldy Gábor - Toldy Construct
3/27/20255 min read

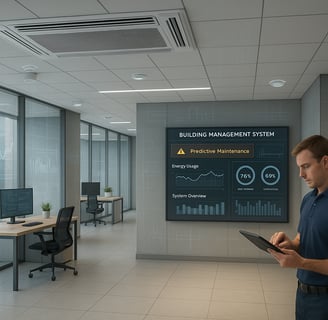
Introduction – A Modern Building Is Not a House, but a System
Today's buildings are no longer passive spatial objects but actively responsive, data-driven systems. A modern office building or hospital now generates more data than an entire small company's IT infrastructure did a decade ago. HVAC systems, elevators, security devices, and energy distribution units all send real-time data to building management systems, increasingly analyzed by AI algorithms. This data intensity opens new opportunities for facility management: predictive maintenance, energy optimization, and enhanced user comfort.
But where are the limits? At what cost? And crucially: How is this different from past technocratic promises? The answer is that artificial intelligence not only automates but also learns, fundamentally transforming industry perspectives.
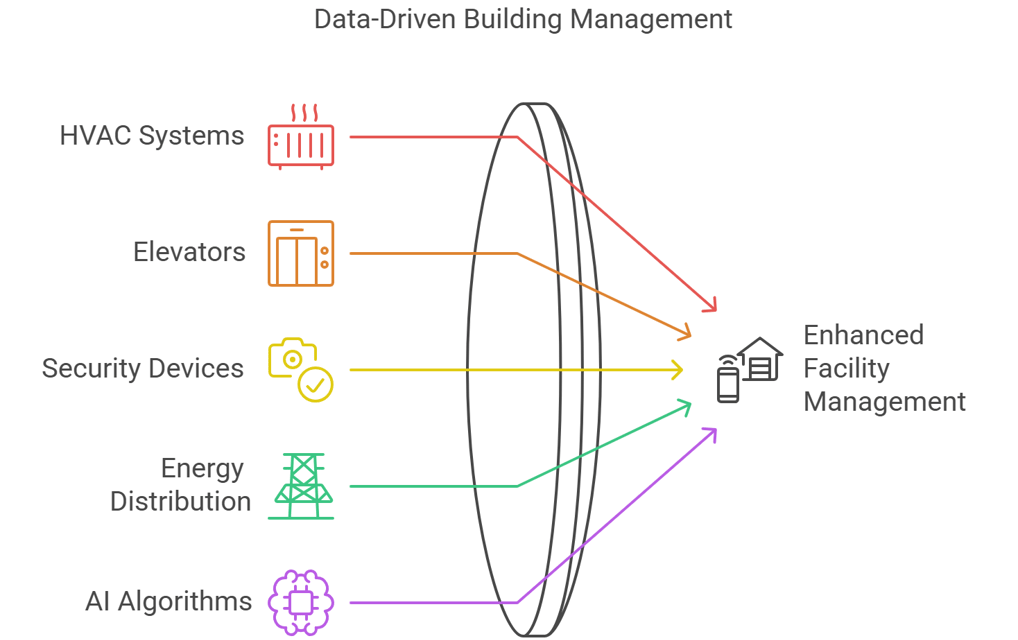
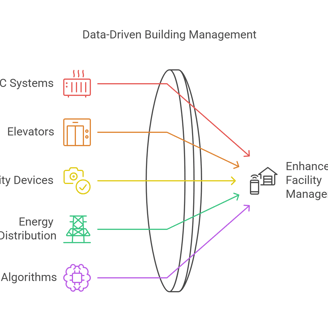
What Is Predictive Maintenance and Why Is It Revolutionary?
Predictive maintenance represents the highest level of operational strategies. It is condition-based rather than scheduled. It does not wait for failures; instead, it calculates their probability. For instance, a cooling compressor is replaced not when it fails—potentially during peak summer temperatures—but when sensor data indicates critical signs such as increased vibrations, electrical consumption, or heat production. This significantly reduces unexpected downtimes, optimizes spare parts inventory, and extends equipment lifespan.
AI not only analyzes data but also detects anomalies that human eyes would miss. While predictive maintenance itself is not new, AI and cloud-based analytics make it genuinely effective and practical for everyday operations.
Case Study: Carnegie Mellon University – Siemens
Provider/Platform: Siemens Desigo CC building management system and Navigator cloud platform.
Problem: Reactive maintenance was costly across a vast campus of over 140 buildings, energy use was suboptimal, and comfort issues (heating/cooling) were frequent. Maintenance tasks were difficult to prioritize due to limited resources.
Solution: Sensor data from HVAC and other systems were collected. Siemens’ cloud platform used AI algorithms (Fault Detection and Diagnostics - FDD) to analyze data, identifying hidden faults, underperforming equipment, and operational anomalies before they became critical issues. The system prioritized tasks for the maintenance team.
Results (According to Siemens Reports):
Significant annual energy savings (millions of USD).
Increased maintenance efficiency.
Reduced comfort complaints.
Potentially extended equipment lifespan through early interventions.
Source: Siemens website (Case Studies, Building Technologies)
Case Study: Microsoft Campus Redmond – In-House Development / Partners
Provider/Platform: Microsoft’s proprietary IoT and Azure-based solutions (Azure Digital Twins, Azure ML) in collaboration with partners like Johnson Controls.
Problem: Managing a large campus of more than 125 buildings was extremely complex. Goals included maximizing energy efficiency, reducing operational costs, enhancing employee comfort, and minimizing environmental footprint.
Solution: Thousands of sensors were installed, collecting real-time data on HVAC, lighting, and other systems. Data analysis through AI algorithms on the Azure platform predicts failures and continuously optimizes energy use based on occupancy, external temperature, and other factors. The "Digital Twin" concept created virtual representations of buildings for simulation and analysis.
Results (According to Microsoft Publications):
Significant annual energy savings (millions of USD).
Dramatic improvement in maintenance processes.
Reduced failure rates.
Improved operational and future development decision-making.
Source: Official Microsoft blogs (Azure, IoT), Microsoft Customer Stories, Smart Building Conference
Case Study: PENN Medicine – Clockworks Analytics
Provider/Platform: Clockworks Analytics (cloud-based FDD and analytics platform).
Problem: Reliable operation of HVAC and other critical systems in hospitals is crucial for patient safety and comfort. Unexpected failures are unacceptable, and energy costs are high. Manual inspections of complex systems were challenging.
Solution: Clockworks Analytics continuously analyzes existing Building Automation System (BAS) data through AI and engineering rules. It identifies hidden operational issues, energy waste, and prioritizes maintenance tasks based on urgency and impact, providing detailed diagnostics.
Results (According to Clockworks Analytics Case Study):
Early detection of an impending bearing failure in a ventilation system allowed scheduled replacement, avoiding costly emergency repairs.
Identified multimillion-dollar operational and energy cost savings across the portfolio.
Increased proactivity in maintenance teams, shifting from emergency repairs to planned maintenance.
Improved compliance with stringent hospital environmental standards (temperature, humidity, air exchange).
Source: Clockworks Analytics website (Case Studies, Resources), articles in Healthcare Facility Management
Data Is Key – Sensors and IoT
The accuracy of predictive models depends heavily on data. Modern building sensor networks collect data from hundreds to thousands of points: temperature, humidity, CO₂, vibration, pressure, electrical consumption, and even sound samples feed into AI systems. The challenges include timely data processing, identifying faulty sensors, and determining the right level of redundancy.
Sensor data processing can occur locally (edge computing) or in the cloud—each with trade-offs. Local processing is faster but limited, while cloud solutions offer broader pattern recognition. The optimal solution typically combines both.
Humans vs. Algorithms – Required Skills
Technology does not replace humans; it reshapes their roles. Maintenance workers must evolve into data analysts; engineers into digital managers. Future professionals must understand AI-driven predictions, not just repair machinery.
This shift raises educational questions. Current vocational training in Hungary does not adequately address digital maintenance and operational needs. Without adaptation, advanced systems will be ready but lack qualified operators.
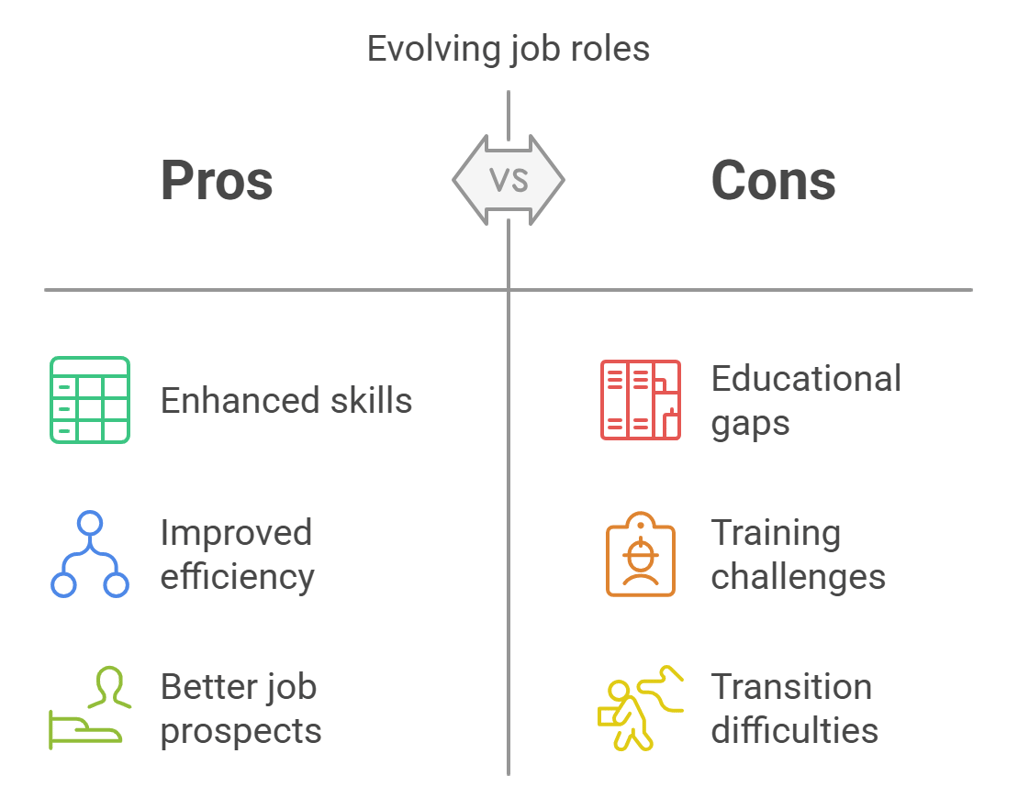
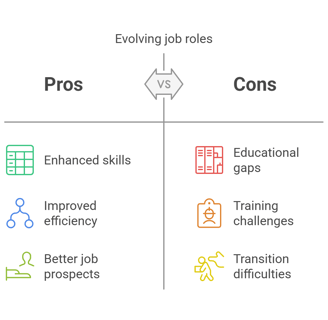
Integration and Challenges – Technology Isn’t Magic
Predictive maintenance technology exists, but system integration remains a significant barrier. Most Building Management Systems (BMS) use closed, outdated protocols that are difficult to link with open AI platforms. Data structuring, synchronization, and historical accessibility often lack.
Predictive systems also raise data security concerns since sensor data can reveal building usage patterns—critical from security and privacy perspectives. Adequate encryption, access control, and audits are essential.
Critical Perspectives – Why Isn’t This More Common?
In Hungary, investing in predictive systems remains "extra," not a standard requirement. This is due not only to upfront costs but also to a CAPEX-centric mindset ignoring OPEX savings. Many decision-makers lack operational expertise or incentives to reduce future risks. Despite evidence that predictive systems outperform traditional maintenance approaches regarding ROI, NPV, and Life Cycle Cost, structural issues persist.
Moreover, building designs often neglect easy maintainability, future accessibility, or simple parts replacement, prioritizing aesthetics over ergonomics and operational efficiency.
Changing the mindset of investors and designers is necessary to fully realize the potential of AI technologies throughout intelligent buildings' lifecycles.
Future articles will explore these themes—particularly the economic impacts of ROI, NPV, LCC, and design errors—in greater depth.
Conclusion – The Future Is Already Here, but Many Have Not Yet Adopted or Recognized This Opportunity
AI-based predictive maintenance isn't just clever; it's essential for 21st-century facility management. Energy efficiency, operational reliability, longer equipment lifespans, and reduced maintenance risks aren't empty slogans—they're measurable outcomes. Those who adopt it gain competitive advantages, while those who delay will fall behind.
The real question isn't whether we can afford predictive systems but whether we can responsibly manage future intelligent buildings without them.
Construction
With over 20 years of experience in general contracting, our company specializes in the flawless execution of unique, bespoke buildings. Our innovative methods and mindset make us stand out in the market.
Our services
Contacts
company@toldyconsult.hu
+36 30 289 2383
© 2024. All rights reserved.
Our WEBPAGES
www.toldyconsult.hu